As an industrial designer, one must always balance both aesthetics and manufacturability when creating the earphones. The goal is to design the earphone that not only looks innovative but also ensures that the production process runs smoothly. However, these two objectives can sometimes conflict with each other, especially when it comes to earphone tooling/mold, design, and development.
Today, let’s focus on the relationship between design aesthetics and manufacturability, specifically discussing the concept of “parting lines” and how it impacts earphone production.
What Are Parting Lines?
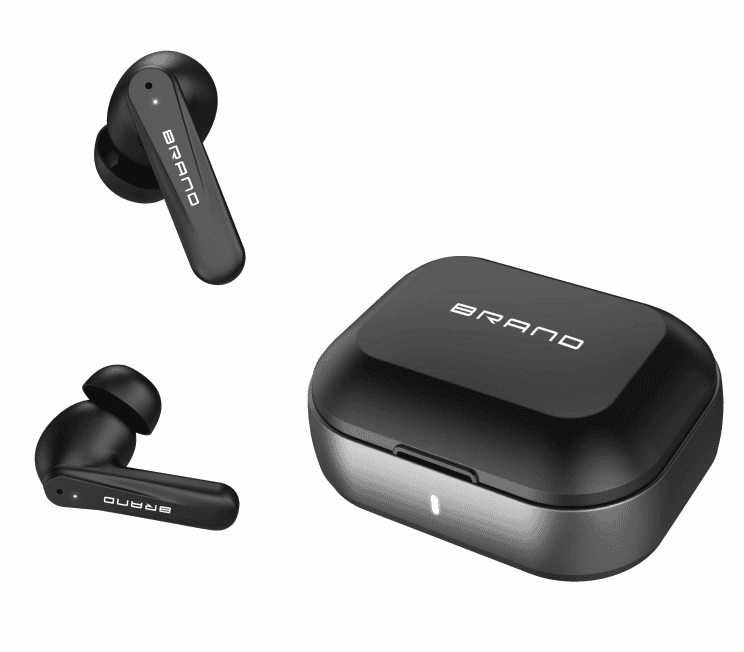
First, let’s take a closer look at what parting lines actually are.
In simple terms, parting lines are the result of the molding process. Most molds used for injection molding are made up of several parts that fit together. Since it’s impossible to make the seams of these parts perfectly smooth, tiny gaps will inevitably appear. During the injection process, these seams create small raised edges at the junctions, which are known as parting lines.
If you observe closely, you’ll notice a faint line on many components—this is the parting line. It’s often found at the edges of parts or at the highest points of a component, where the mold separates. The location of the parting line is typically at the junction between two parts, and designers can creatively use different colors or materials to enhance the aesthetics.
When done well, the parting line not only helps the earphone tooling and manufacturability but also elevates its overall visual appeal. The optimal design of parting lines can make a product feel more refined and polished. As a designer, mastering the principles of parting lines is crucial, as it allows you to express your creativity while enhancing the product’s form and function.
The Issue of “Inability to Demold” in Earphone Design
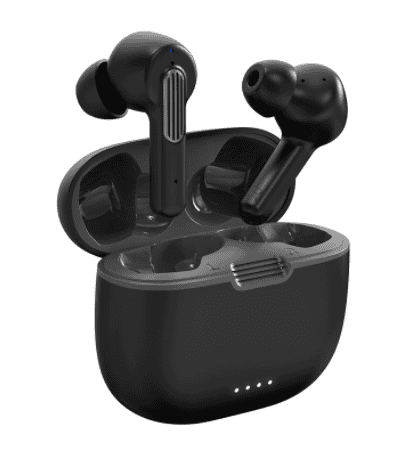
When designing earphones, particularly in the realm of manufacturing, the challenge of “demolding” becomes an unavoidable consideration. This issue arises when the design of the product does not allow for easy separation from the mold during the manufacturing process. To resolve this, adjustments must often be made to the earphone’s exterior appearance to ensure it is easier to demold.
If you leave this issue solely to the engineers, there’s a high likelihood that your original earphone design will be “rewritten,” and the final product may not reflect the aesthetic you envisioned. It’s important to remember that this is an issue rooted in the initial design phase—one that can impact the visual appeal and functionality of the product.
The Role of the Designer in Earphone Development
As a seasoned industrial designer at Digcue, your job isn’t just about creating an eye-catching product; it’s about solving these manufacturability issues early on. By leveraging your design experience, you can resolve demolding challenges while seamlessly integrating parting lines into the overall earphone design.
The goal is to create a product that can be easily manufactured without compromising its visual appeal. This requires a deep understanding of how molds work and how design choices can influence the production process.
Conclusion: A Balance of Aesthetics and Practicality in Earphone Tooling
In the world of B2B earphone manufacturing, where precision and functionality are key, it’s essential to work closely with engineers from the outset. Your role as a designer is to ensure that your earphone designs are both beautiful and producible, allowing your clients to benefit from high-quality, visually appealing products that meet manufacturing standards.
At Digcue, we take pride in providing tailored B2B earphone solutions that prioritize both design excellence and efficient manufacturability. Our experienced design team works alongside engineers to ensure that each product not only meets the highest aesthetic standards but is also easy to produce at scale.
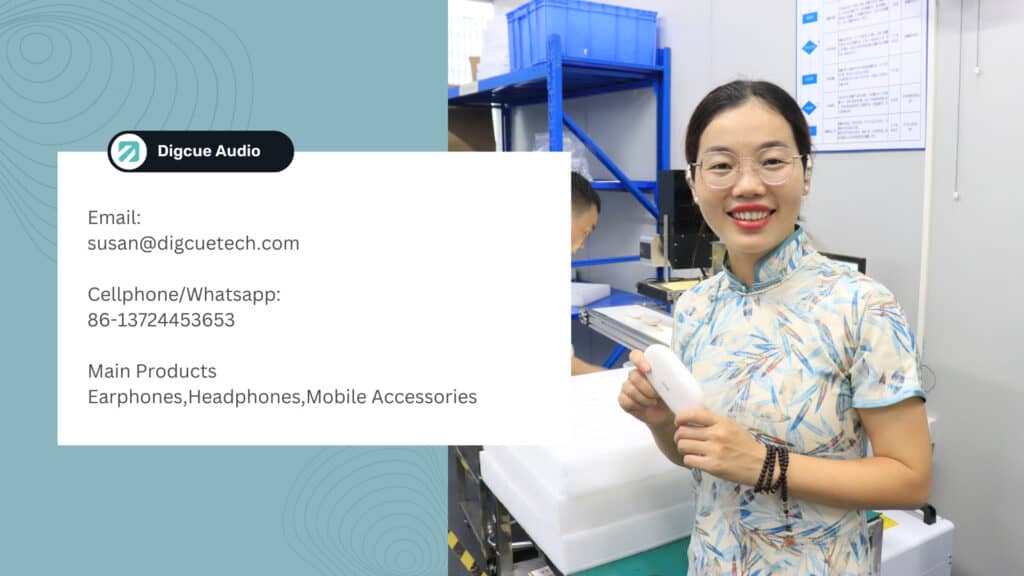